What is custom injection molding?
The initial question that comes to mind on hearing the terms Custom injection molding is what is custom injection moldering. This term refers to the making of plastic parts for specific applications i.e. customizing the parts as per the customer’s needs.
Injection molding of custom plastic parts
Injection molding is a process in which plastic pellets are injected and melted under high force into a mold cavity. The molded parts are then ejected, and the process repeated. The finished items can then be used as is, or as a part of other products. To do so needs an injection molding tooling and machine. The molding machine consists of a clamping unit to close and open the mold mechanically, and an injection unit to heat and inject the material into the closed mold. Injection molding utilizes extremely high forces and typically the machine is hydraulic or electric. Tooling for production injecting molding applications must be capable to survive under high force and is made from aluminum or steel. The potentially high cost of tooling generally drives the economics of a plastic molding application. Injection molding is a perfect way to make custom plastic molding parts.
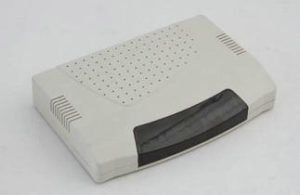
The process is broken down
There are 3 main parts of the injection molding process. The injection apparatus itself which melts and then passes on the plastic, the plastic mold, which is custom made, and clamping to provide controlled force. The mold is a specially designed tool with a base one or more cavities that will eventually be packed with resin. The injection unit melts the plastic granules and then injects them into the mold by either a ram injector or a reciprocating screw. The reciprocating screw provides the capability to inject little amounts of resin in the total shots, which is excellent for producing little parts. After injection, the mold is chilled constantly until the resin reaches a temperature that permits it to solidify.
Complications with injection molding
Injection molding problems are few and can be simply rejected by paying close focus to the design of the plastic mold, the process itself and caring for your equipment. Parts can be scorched or burned when the temperature is very high, which is sometimes caused by the length of the cycle time which may be too long. This causes the resin to heat high. Wrapping of parts occurs when there is an uneven surface temperature for the molds. Surface imperfections occur when the melt temperature is too high, which causes the resin to break down and generate the gas.